The only Nerf bars I really like are the XRF Pro Pegs from eBay but at near $300 are pricey. I didn't want to pay $100-$150 for ones that I didn't really like and couldn't make myself let go of $300 for the ones I do like but need Nerf bars, so I thought I give a try at modding a set that are from an LTR450. The bars a Bling Star brand, given to me for some work I did to the LTR450. They were, of course, much too long to mount to the foot peg like normal but with some cutting I got them positioned between the wheels. I cut 4" off the back and 3" off the front tubes where they meet the frame. With the front bar being on an angle, making them narrow makes them shorter too. The rear meets the frame about an inch below and 5" behind the front foot peg bolt. I could weld an extension to the peg/brake lever mounting plate but making a new one seemed to be a better option and it would allow me to lower the pegs an inch for a little more leg room. I've found using easy to work it materials for mock up to make things much easier, so here it is (OSB for mounting plates, plastic wedges for foot pegs, pieces of broom handle the right diameter that fits tight into the tubes and half in bolts for brake lever pivot. At work we have a place that does laser burning for us. I'll have the mounting plates done there. Had planned to make the pegs from billet but looking at some of the aftermarket quad pegs I might go with welded plate. Here's some pictures of the mock up and the CAD drawing of the plates I'll have burned and a model of the pegs if I do use billet.
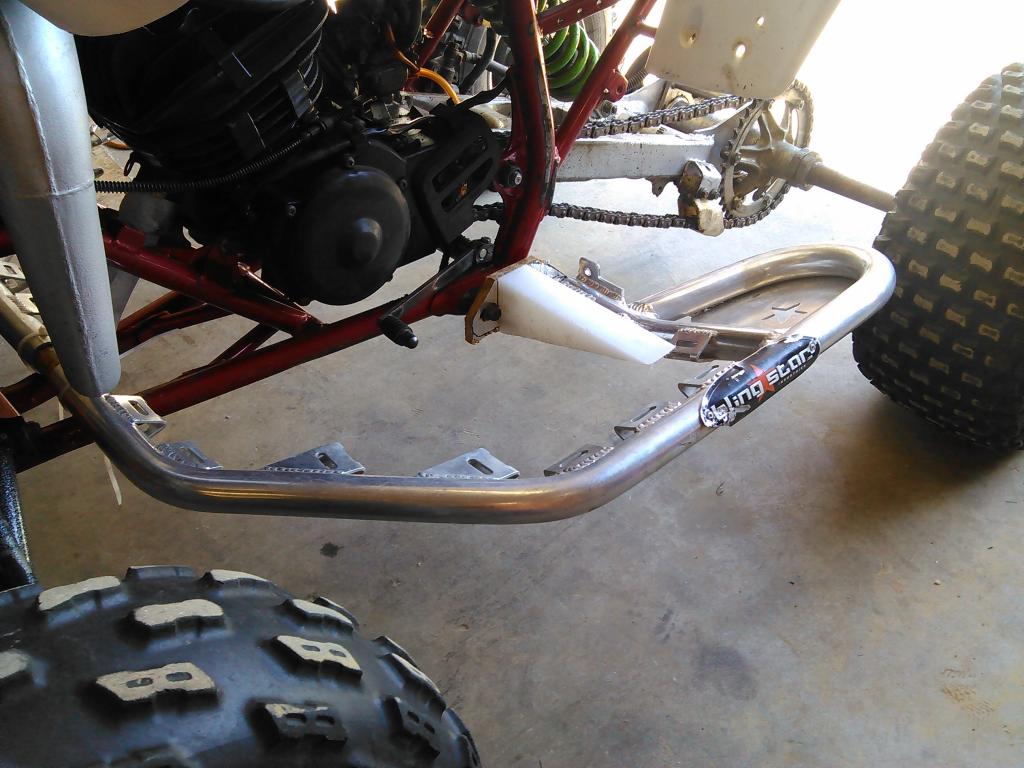

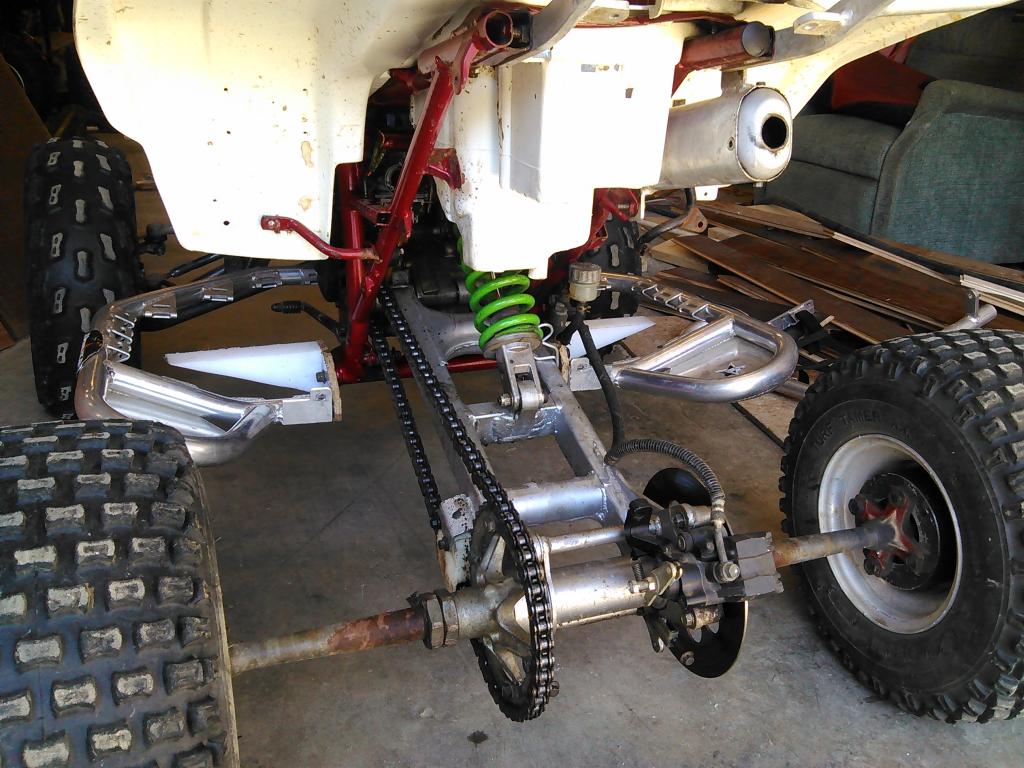
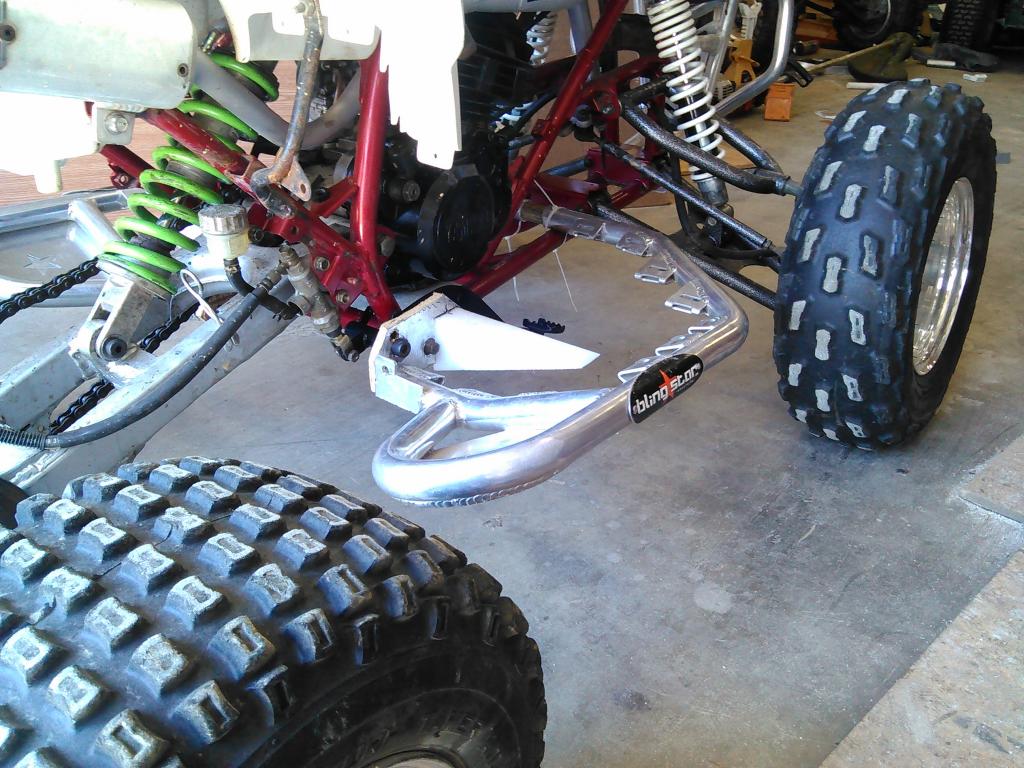





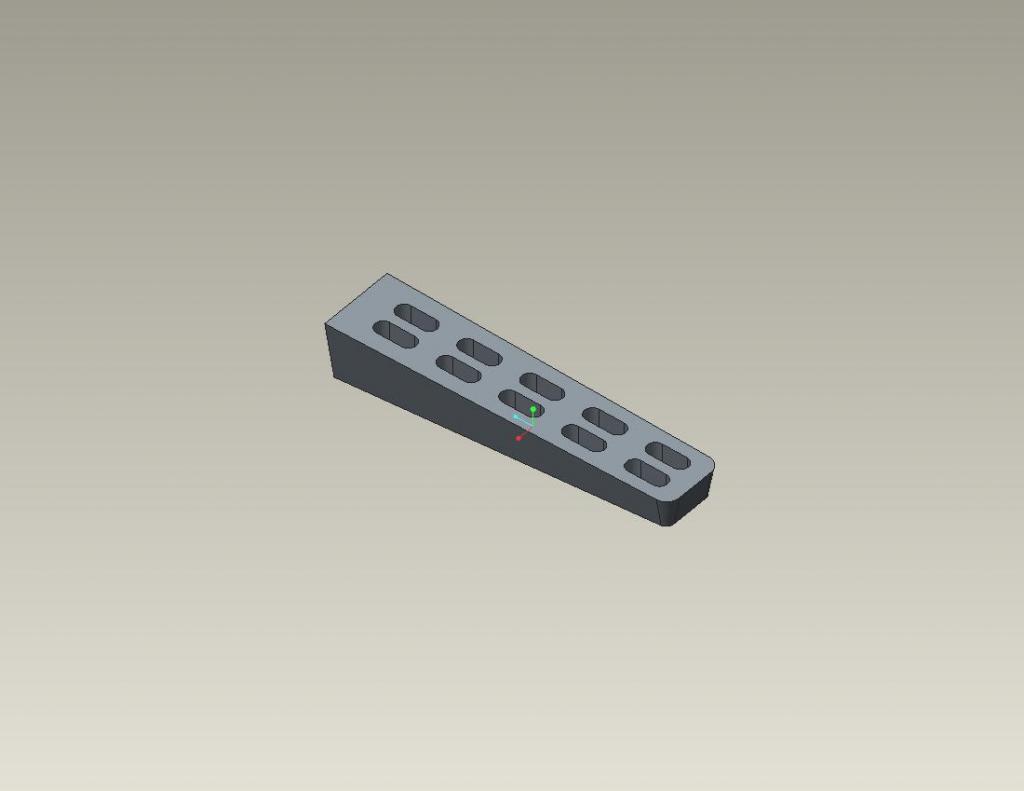
Forgive the mess I've let me shop get to. The last 6 months I spent remodeling a house I inherited to rent and everything from the house and extra material has just been piled into my shop, can't move around or find anything. Meant to get it back in order this weekend but worked on quads instead. Just needing to work on something fun for a little while.
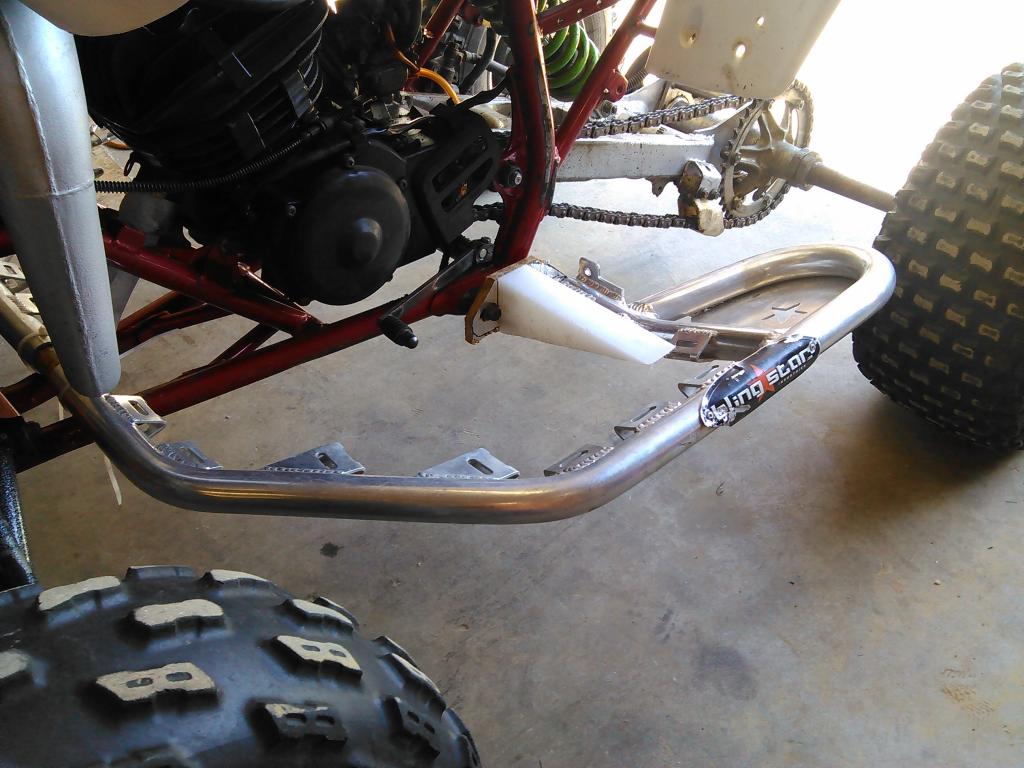

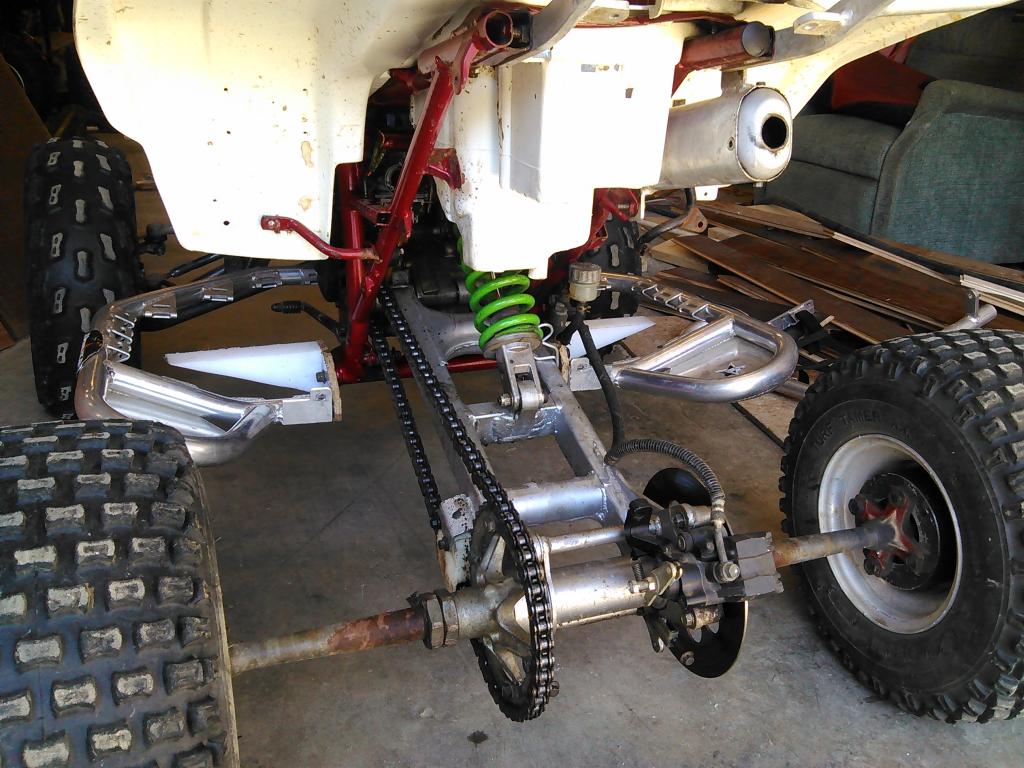
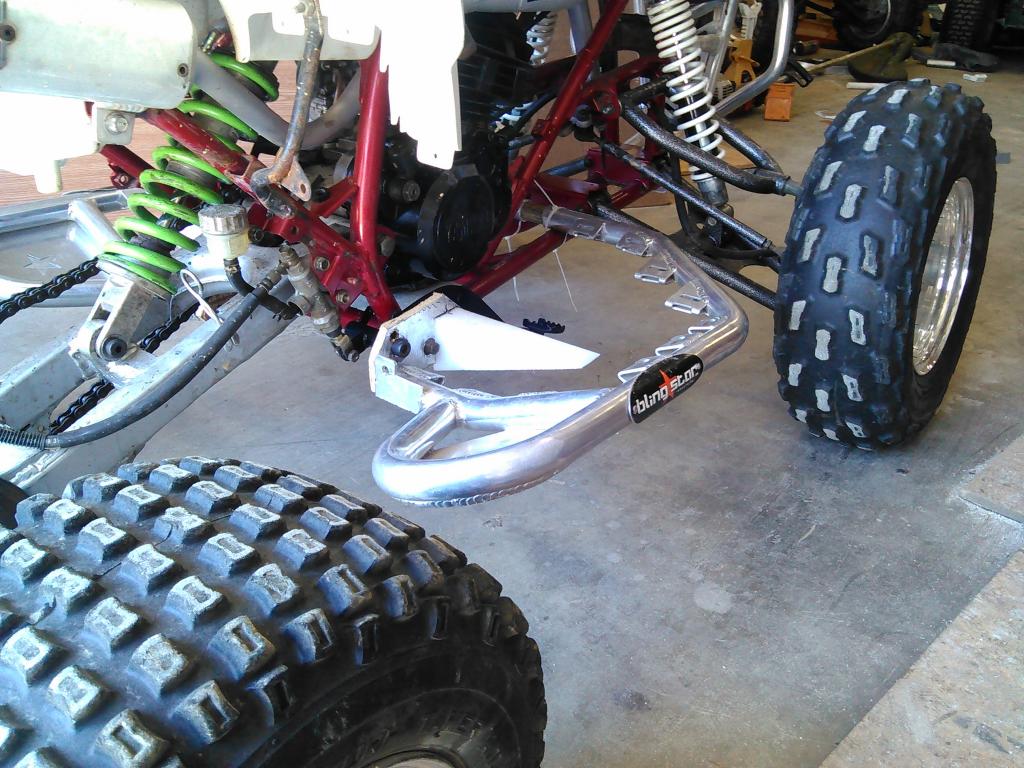





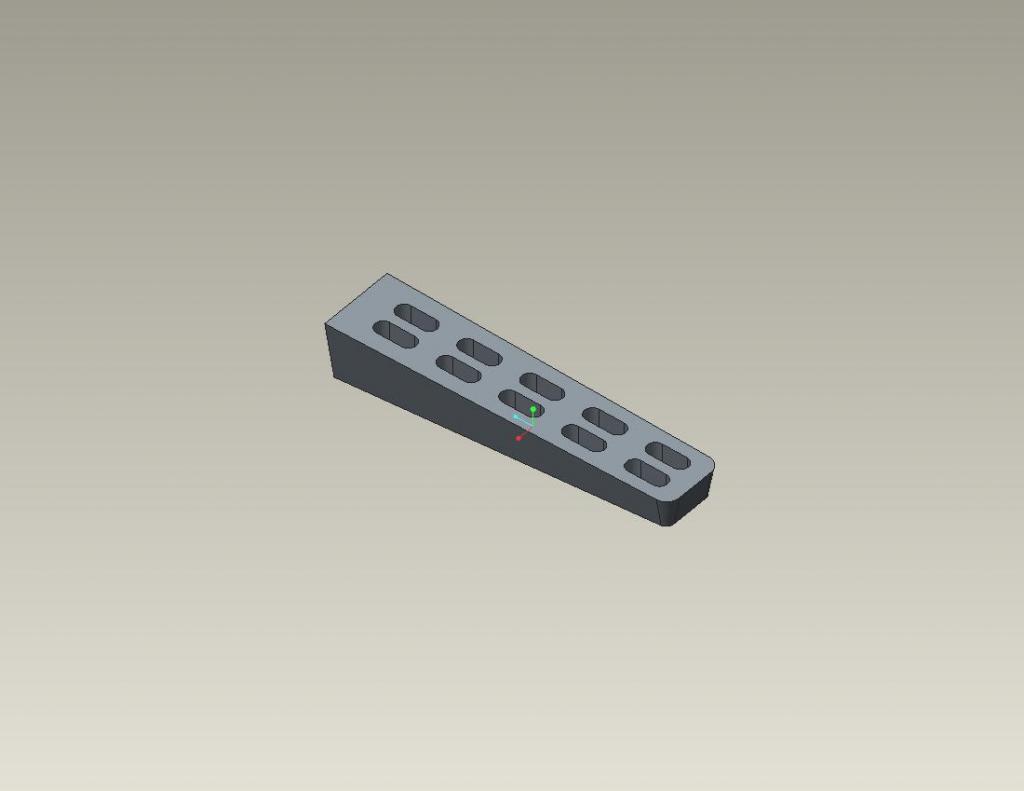
Forgive the mess I've let me shop get to. The last 6 months I spent remodeling a house I inherited to rent and everything from the house and extra material has just been piled into my shop, can't move around or find anything. Meant to get it back in order this weekend but worked on quads instead. Just needing to work on something fun for a little while.